Der aktuelle Stand der Technik ermöglicht es uns, einen Großteil der bekannten Stähle und Legierungen stofflich zu verbinden. Jeder Anwendungsfall verlangt andere Verfahren, Einstellungen, Zusätze, Schutzgase und Schutzkleidung. Selbst die Anforderungen an die unmittelbare Umgebung unterscheiden sich je nach Schweißverfahren deutlich voneinander.
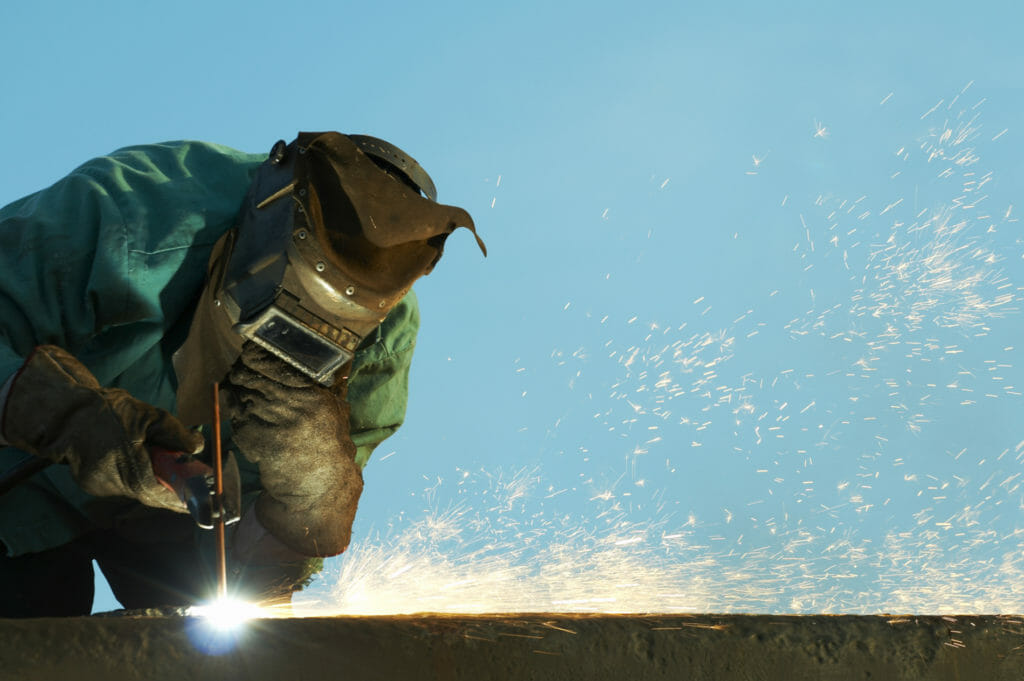
Um zu verstehen, warum sich bestimmte Verfahren für konkrete Anforderungen besser oder schlechter eignen, ist es notwendig, diese genauer zu betrachten und einzuordnen.
Themen im Überblick
- Die Schweißverfahren in kurzer Übersicht
- Schweißverfahren Nummern nach DIN EN ISO 4063
- Gasschweißen – das älteste Schweißverfahren
- Lichtbogenhandschweißen – simpel, aber effektiv
- MIG/MAG-Schweißen – mit Schutzgasen zur perfekten Schweißnaht
- WIG-Schweißen – Für ruhige Hände und viel Übung
- Bolzenschweißen – wie man Bolzen unlösbar
- Laserschweißen – längst keine Science-Fiction mehr
- Formieren (Wurzelschutz)
- Das Unterpulverschweißen – Schweißverfahren mit Pulverzugabe
- Das Widerstandsschweißen
- Welche persönliche Schutzkleidung (PSA) benötige ich für welches Schweißverfahren?
- Welche Schweißverfahren benötigen Schutzgas?
- Geeignete Schutzgase zum Schweißen nach ISO 14175
Die Schweißverfahren in kurzer Übersicht
Schweißen mittels Gasgemisch aus Sauerstoff und Acetylen. Eine bis zu 3000 °Celsius heiße Flamme schmilzt den Grundwerkstoff auf.
Eine Stabelektrode entzündet bei Berührung des Werkstücks einen Lichtbogen. Die Umhüllung verdampft und fungiert als Schutzgas.
Verfahren mittels inerten oder aktiven Schutzgasen und automatischer Zuführung des Schweißdrahtes, welcher bei Berührung des Werkstücks einen Lichtbogen entzündet.
Zum Verschweißen von bolzenartigen Elementen. Ein Lichtbogen zwischen Werkstück und Stirnfläche des Bolzens verflüssigt beide kurzzeitig, wodurch eine stoffliche Verbindung entsteht.
Gebündeltes Licht sorgt bei geringer Wärmeeinwirkung auf das Bauteil für dessen Aufschmelzen und Verbindung. Dieses Verfahren wird häufig vollautomatisiert angewendet.
Ein Lichtbogen wird unter Zuführung grobkörnigen Pulvers gezündet, um Werkstücke besonders schnell zu verschweißen.
Verfahren ohne Zusatz und Schutzgas durch Wärme und Druckeinwirkung mittels Elektroden.
Schweißverfahren Nummern nach DIN EN ISO 4063
Basierend auf der Norm DIN EN ISO 4063 gibt es ein Ordnungsnummernsystem im Schweißen, welches gute Koordination und Abstimmung von Schweißarbeiten ermöglicht. Gerade in weltweit agierenden Unternehmen und bei starker internationaler Zusammenarbeit wird die Bedeutung der Prozessnummern beim Schweißen immer wichtiger.
Kennzahl | Nummer | Schweißverfahren |
111 | Lichtbogenhandschweißen |
112 | Schwerkraftlichtbogenschweißen |
114 | Metall-Lichtbogenschweißen mit Fülldrahtelektrode (ohne Gasschutz) |
121 | UP-Schweißen mit Massivdrahtelektrode |
122 | UP-Schweißen mit Massivbandelektrode |
124 | UP-Schweißen mit Metallpulverzusatz |
125 | UP-Schweißen mit Fülldrahtelektrode |
126 | UP-Schweißen mit Füllbandelektrode |
131 | Metall-lnertgasschweißen mit Massivdrahtelektrode |
132 | Metall-Inertgasschweißen mit schweißpulvergefüllter Drahtelektrode |
133 | Metall-Inertgasschweißen mit metallpulvergefüllter Drahtelektrode |
135 | Metall-Aktivgasschweißen mit Massivdrahtelektrode |
136 | MAG-Schweißen mit schweißpulvergefüllter Drahtelektrode |
138 | Metall-Aktivgasschweißenmit metallpulvergefüllter Drahtelektrode |
141 | Wolfram-Inertgasschweißen (WIG) mit Massivdraht |
142 | WIG-Schweißen ohne Schweißzusatz |
143 | WIG-Schweißen mit Fülldraht- oder Füllstabzusatz |
145 | WIG-Schweißen mit reduzierenden Gasanteilen und Massivdrahtzusatz |
146 | WIG-Schweißen mit reduzierenden Gasanteilen und Fülldrahtzusatz |
147 | WIG-Schweißen mit aktiven Gasanteilen |
151 | Plasma-Metall-Schutzgasschweißen |
152 | Pulver-Plasma-Lichtbogenschweißen |
153 | Plasma-Stichlochschweißen |
154 | Plasma-Strahlschweißen |
155 | Plasmastrahl-Plasmalichtbogenschweißen |
211 | Indirektes Widerstandspunktschweißen |
212 | Direktes Widerstandspunktschweißen |
221 | Überlapp-Rollennahtschweißen |
222 | Quetschnahtschweißen |
223 | Rollennahtschweißen mit Kantenvorbereitung |
224 | Rollennahtschweißen mit Drahtelektrode |
225 | Folienstumpfnahtschweißen |
226 | Folien-Überlappnahtschweißen |
231 | Einseitiges Buckelschweißen |
232 | Beidseitiges Buckelschweißen |
241 | Abbrennstumpfschweißen mit Vorwärmen |
242 | Abbrennstumpfschweißen ohne Vorwärmen |
25 | Pressstumpfschweißen |
26 | Widerstandsbolzenschweißen |
27 | Widerstandspressschweißen mit Hochfrequenz |
311 | Gasschweißen mit Sauerstoff-Acetylen-Flamme |
312 | Gasschweißen mit Sauerstoff-Propan-Flamme |
313 | Gasschweißen mit Sauerstoff-Wasserstoff-Flamme |
41 | Ultraschallschweißen |
42 | Reibschweißen |
421 | Reibschweißen mit kontinuierlichem Antrieb |
422 | Reibschweißen mit Schwungradantrieb |
423 | Reibbolzenschweißen |
43 | Rührreibschweißen |
441 | Sprengschweißen |
442 | Magnetimpulsschweißen |
45 | Diffusionsschweißen |
47 | Gaspressschweißen |
48 | Kaltpressschweißen |
49 | Heißpressschweißen |
51 | Elektronenstrahlschweißen |
511 | EB-Schweißen unter Vakuum |
512 | EB-Schweißen in Atmosphäre |
513 | EB-Schweißen unter Schutzgas |
521 | Festkörper-Laserstrahlschweißen |
522 | Gas-Laserstrahlschweißen |
523 | Dioden-Laserstrahlschweißen / Halbleiter-Laserschweißen |
71 | Aluminothermisches Schweißen |
72 | Elektroschlackeschweißen |
721 | Elektroschlackeschweißen mit Bandelektrode |
722 | Elektroschlackeschweißen mit Drahtelektrode |
73 | Elektrogasschweißen |
741 | Induktives Stumpfschweißen |
742 | Induktives Rollennahtschweißen |
743 | Induktives Hochfrequenzschweißen |
753 | Infrarotschweißen |
783 | Bolzenschweißen mit Hubzündung |
784 | Kurzzeit-Bolzenschweißen mit Hubzündung |
785 | Kondensatorentladungs-Bolzenschweißen mit Hubzündung |
786 | Kondensatorentladungs-Bolzenschweißen mit Spitzenzündung |
787 | Bolzenschweißen mit Ringzündung |
8 | Schneiden und Ausfugen |
9 | Hartlöten, Weichlöten und Fugenlöten |
Gasschweißen – das älteste Schweißverfahren
Das Gasschmelzschweißen, mittels Sauerstoff-Acetylen-Gemisch und einer Flamme von bis zu 3000 °Celsius war revolutionär. Es eröffnete Ingenieuren Ende des 19. Jahrhunderts ungeahnte Möglichkeiten, ihre Konstruktionen auszulegen.
Autogenschweißen ist relativ einfach und nahezu überall einsetzbar. Es findet auch heute noch häufige Anwendung auf Baustellen und im Handwerk.
Es wird hauptsächlich zum Schweißen von Metallen angewendet. Bei dieser Art des Schweißens wird der zu bearbeitende Werkstoff durch Hitzeeinwirkung geschmolzen. Die nötige Wärme-Energie für das Autogenverfahren wird durch das Verbrennen eines Brenngases mit Sauerstoff gewonnen, weshalb technische Gase eine zentrale Bedeutung für das Autogenschweißen haben. Hierfür werden in den meisten Fällen Brenngase wie Acetylen oder Propan verwendet, da diese Gase eine hohe Effizienz besitzen und eine schnelle Schnittgeschwindigkeit ermöglichen.
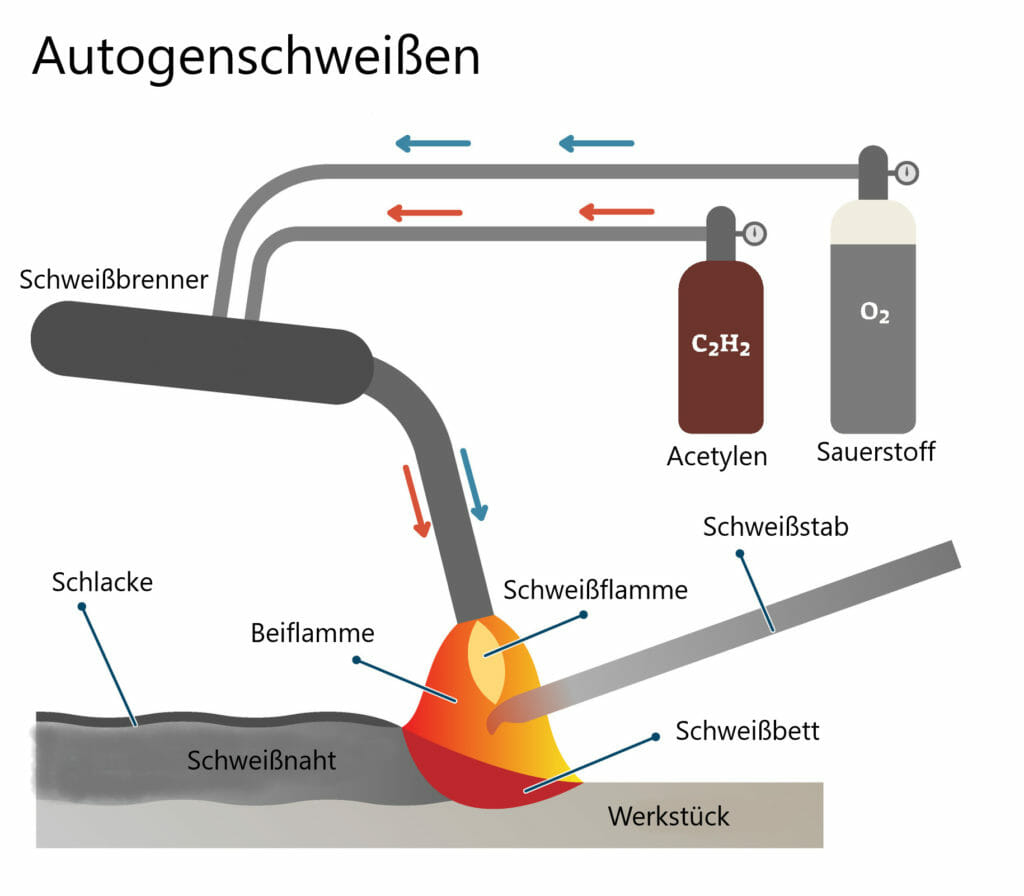
Zwei Gasflaschen mit reinem Sauerstoff und Acetylen sind durch zwei Schläuche mit einem Handbrenner verbunden. Dieser arbeitet nach dem Injektorprinzip: Eine Mischdüse lässt Sauerstoff innen schnell hindurchströmen, was eine Sogwirkung auf das Acetylen im äußeren der Düse ausübt. Der Schweißer stellt das Gasgemisch durch zwei Ventile entsprechend ein, zündet die Flamme und beginnt das zu fügende Material zu schmelzen. Dabei ist er in der Lage, einen Zusatz in Drahtform per Hand hinzuzugeben und auch größere Spalte zu überbrücken.
Lichtbogenhandschweißen – simples, aber effektives Schweißverfahren
Die industrielle Produktion elektrischen Stroms ermöglichte das Schweißen mittels Lichtbogen. Anfänglich noch durch zwei Kohleelektroden umgesetzt, nutzen Schweißer heute Drahtelektroden mit Umhüllung.
Wie funktioniert das E-Handschweißen?
Der Schweißer befestigt den Schweißstab, der zugleich auch Elektrode ist, in einer Klemme und verbindet das Werkstück mit einem Massekabel.
Die abschmelzende Stabelektrode entzündet bei Berührung mit dem zu schweißenden Werkstück einen Lichtbogen. Die Inhaltsstoffe der Umhüllung helfen diesen zu stabilisieren und verhindern die Oxidation der Schweißnaht.
Nach dem Auskühlen bildet sich die sogenannte Schlacke auf der Naht, die mithilfe eines spitzen Schlackehammers abzuklopfen, und einer Drahtbürste zu reinigen ist.
Dieses Schweißverfahren benötigt kein zusätzliches Schutzgas, da die Stoffe in der Umhüllung ausreichen, um die Naht vor Verunreinigungen und Einschlüssen zu schützen.
Dadurch bleibt das Gerät kompakt und kann, je nach Ausführung, mit einer Hand getragen werden.
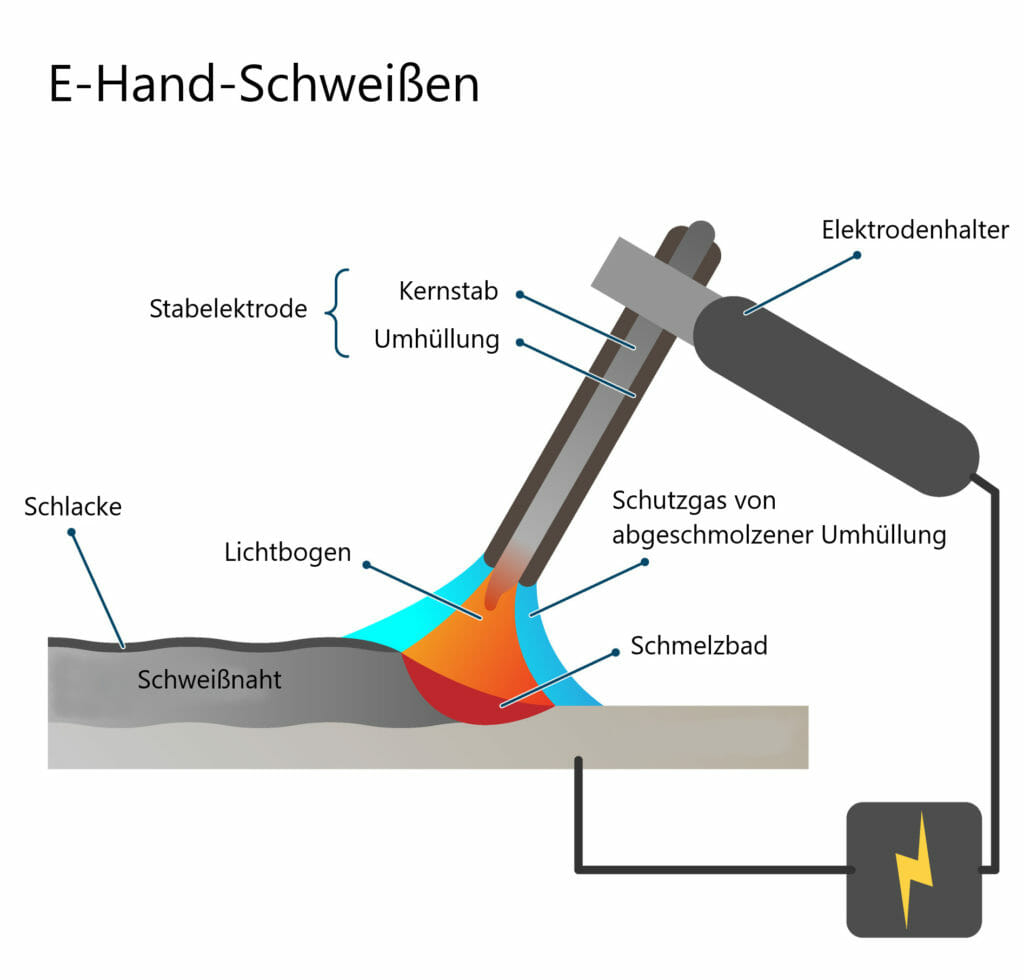
Welche Schweißstäbe benötige ich?
Umhüllte Stabelektroden bestehen aus einem Kernstab und einer vorwiegend mineralischen Umhüllung, die durch Bindemittel am Kernstab haftet.
Die Vielzahl der erhältlichen Schweißstäbe ermöglicht es, beinahe alle erdenklichen Werkstoffe mit diesem Schweißverfahren zu fügen.
Die Schweißstäbe lassen sich nach:
- Umhüllungstyp
- Umhüllungsdicke
- Material
- und Art der Lage
unterscheiden.
Je nach Anwendung muss die richtige Stabelektrode genutzt werden, um saubere Ergebnisse zu erzielen.
Einstellung der richtigen Stromstärke beim E-Handschweißen
Stromstärke (in Ampere) = 30 bis 50 x Kernstabdurchmesser
Die Blechdicken, die sich mittels E-Handschweißen fügen lassen, beginnen etwa bei 1,5 mm und sind rein theoretisch nach oben unbegrenzt. In der Praxis liegt die Grenze bei etwa 100 mm. Für dickere Werkstücke wird mit mehreren Lagen gearbeitet.
Unabhängig vom gewählten Schweißstab und der eingestellten Stromstärke bietet das E-Handschweißen einen entscheidenden Vorteil, den es mit dem Gasschmelzschweißen teilt: Das Verfahren eignet sich hervorragend zum Schweißen im Freien, da es unempfindlich gegenüber Zugwind ist. Nachteilig bei dieser Anwendung ist die notwendige Verfügbarkeit eines ausreichend dimensionierten Stromanschlusses, ist dieser nicht vorhanden, kann man allerdings auch einen entsprechend leistungsfähigen Stromerzeuger mieten.
MIG/MAG-Schweißen – mit verschiedenen Gasen zur perfekten Schweißnaht
Die Entwicklung des MIG/MAG-Schweißens eröffnete wiederum neue Türen. Das Schutzgasschweißverfahren ist einfach zu erlernen und durch die Verwendung von inerten oder aktiven Gasen vergrößert sich die Anzahl der schweißbaren Legierungen immens.
Durch den Handbrenner wird der Schweißdraht, der zugleich Zusatz und Elektrode darstellt, automatisch zugeführt. Eine Düse am vorderen Ende lässt Schutzgas ausströmen, wodurch die Umgebungsluft verdrängt wird.
Das MAG-Schweißen (Metall-Aktivgas-Schweißen) ist die gängigste und am weitesten verbreitete Form des Schweißens mit Industriegasen. Hierbei werden als Aktivgase Kohlendioxid, Wasserstoff oder Sauerstoff Gemische für das Schweißen von legierten und unlegierten Stählen verwendet.
MAG Schweißen zählt zu den Schutzgas Schweißverfahren. Dabei dienen die Industriegase also nicht als Brennstoff, sondern als Schutzgas.
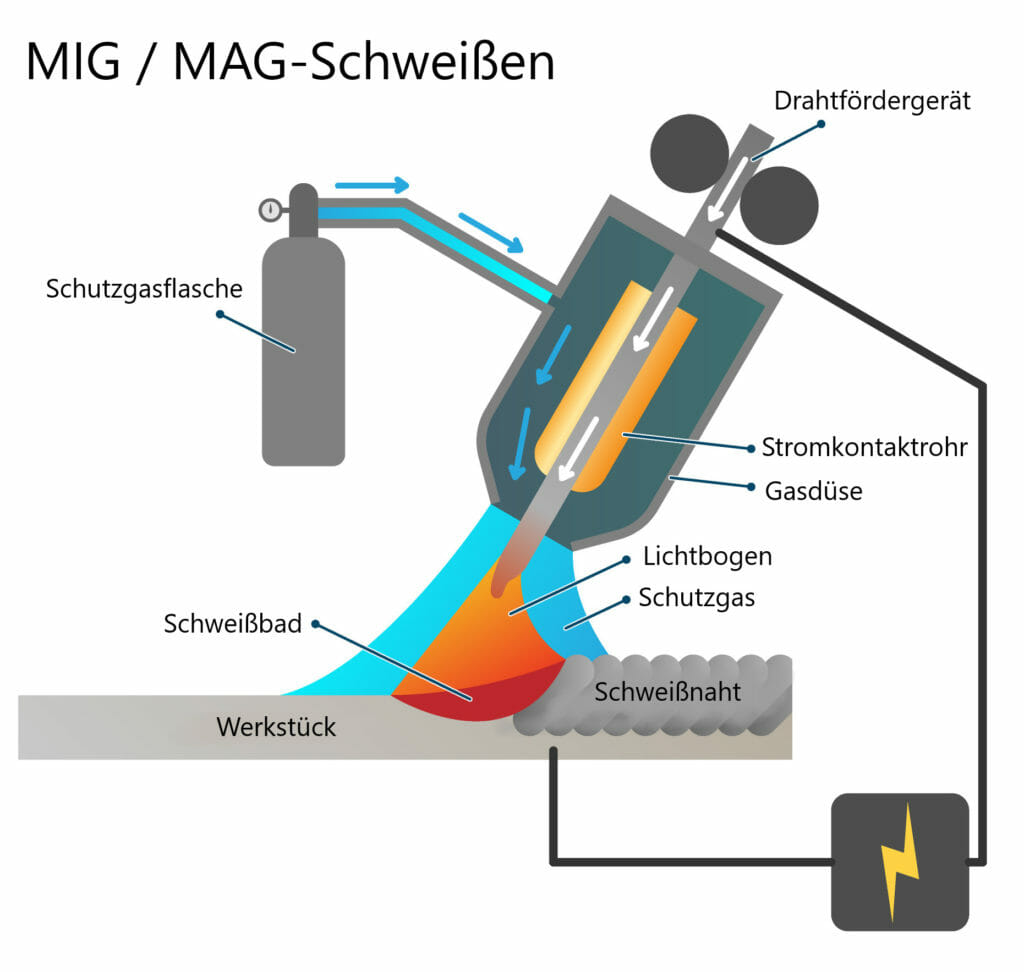
Schutzgase verhindern, dass die Schmelze mit dem Sauerstoff der Luft reagiert. Denn bei einer solchen Oxidation kommt es zur Schlackebildung wodurch die Schweißnaht spröde und anfälliger für Rost ist, da sich durch die löchrige Schweißnaht Feuchtigkeit festsetzen kann. Da der Einsatz des Schutzgases beim MAG Schweißen diese Oxidation verhindert, ist es eine sehr gängige Methode, die unter anderem häufig in der in der Automobilindustrie oder dem Schiffbau eingesetzt wird.
Weitere Merkmale des MAG Schweißens ist eine leichte Handhabung, schnelles Arbeiten, qualitativ hochwertige Ergebnisse und eine hohe Abschmelzleistung.
Das Metall-Inertgas-Schweißen ist eine weitere Variante des Schutzgas-Schweißens. Hierbei wird, im Gegensatz zum MAG Schweißen, mit inaktiven d.h. inerten Gasen gearbeitet. Beim MIG Schweißen werden Industriegase wie Argon und Helium zum Schweißen von hochlegierten Stählen oder Werkstoffen wie Aluminium, Magnesium oder Titan verwendet. Auch beim MIG Schweißen ist das Ziel eine hochwertige Schweißnaht zu erzielen.
WIG-Schweißen – Schweißverfahren für ruhige Hände und viel Übung
Das WIG-Schweißen entstand auf der Suche nach einem Verfahren zum Fügen des leicht entzündlichen Magnesiums. Lichtbogenschweißen mittels Wolframelektrode und zunächst Helium als Schutzgas brachte die Lösung für dieses Problem. Seit dem gilt WIG-Schweißen als Königsdisziplin unter Schweißern und verlangt viel Übung und handwerkliches Geschick.
Beim WIG Schweißen besteht die Elektrode aus hitzebeständigem Wolfram. Dies führt dazu, dass die Elektrode beim Schweißen im Gegensatz zu dem MAG und MIG-Schweißverfahren nicht abschmilzt. Bei dieser Schweißmethode entstehen daher nur wenige Spritzer oder Gase. Ähnlich wie beim MIG Schweißen werden auch beim WIG Schweißen langsam reagierende Gase wie Argon oder Helium verwendet. Das WIG Schweißen wird hauptsächlich zum Schweißen von dünnen Aluminium-Blechen oder Edelstahl eingesetzt, kann aber auch beim Schweißen von Stahlblechen verwendet werden.
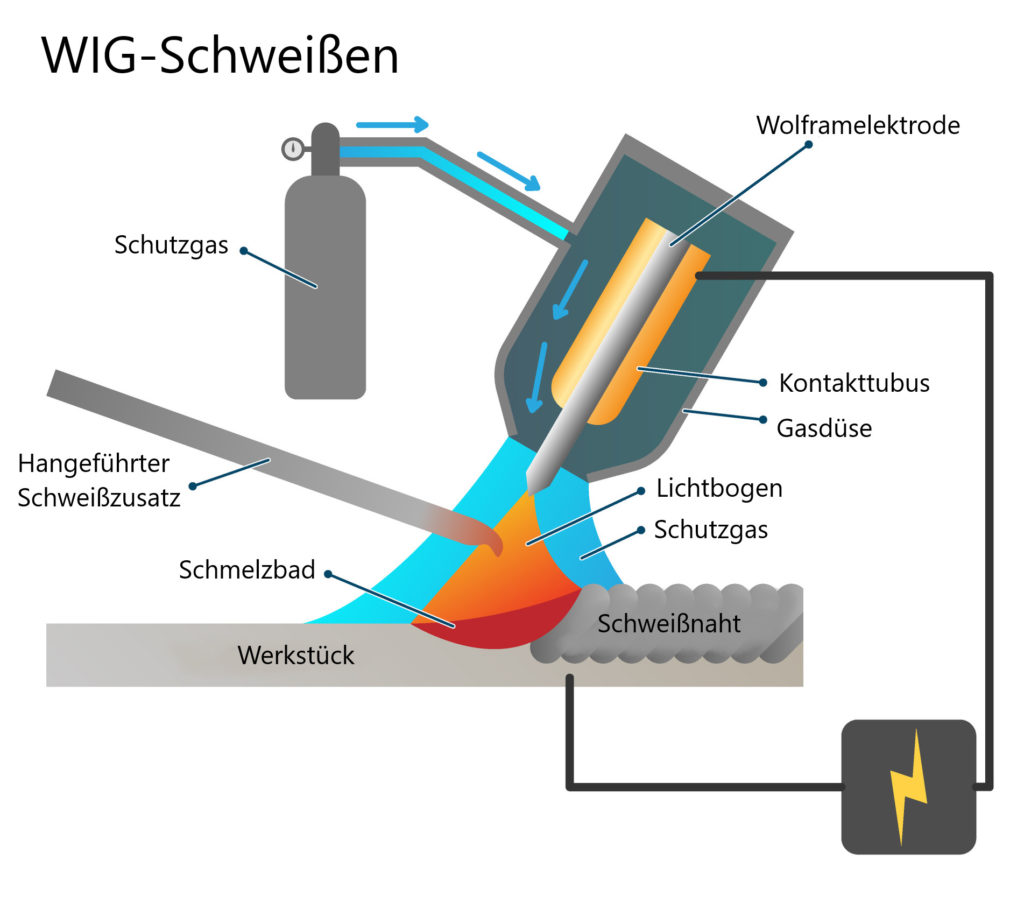
Ein Unterschied gegenüber dem MIG/MAG Schweißen ist, dass das WIG Schweißen deutlich langsamer abläuft. Das Ergebnis kann sich allerdings sehen lassen: Aufgrund der hohen Temperaturen im Lichtbogen schmelzen die Kanten perfekt ineinander, was zu sehr schönen und feinen Schweißnähten führt. Aus diesem Grund wird das WIG Schweißen häufig beim Schweißen von Möbelstücken verwendet. Eben dort, wo die Schweißnaht leicht zu erkennen ist.
Schweißverfahren Bolzenschweißen – wie man Bolzen unlösbar verbindet
Das Lichtbogenbolzenschweißen ist ein Lichtbogenpressschweißverfahren.
Ziel ist es, dass bolzenförmige Teile wie Gewindebolzen, Stifte, Buchsen, Ösen oder Haken eine dauerhafte, unlösbare Verbindung mit anderen Bauteilen eingehen. Ein gezündeter Lichtbogen zwischen Bolzen und Werkstück schmilzt die Fügestellen auf und geringer Anpressdruck bis zum Auskühlen sorgt für eine anschließende stoffschlüssige Verbindung.
Die Produkte, die mittels dieser Schweißtechnik gefertigt werden, finden sich vermutlich auch in Ihrer Küche: Sind die Knäufe auf den Deckeln Ihrer Kochtöpfe nicht sichtbar mit einer Schraube auf diesem befestigt, handelt es sich höchstwahrscheinlich um eine stoffschlüssige Verbindung durch Bolzenschweißen.
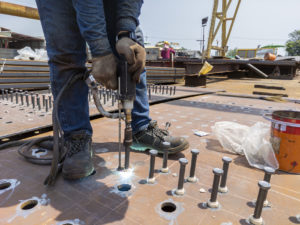
Zu unterscheiden sind das Hubzündungsbolzenschweißen und das Spitzenzündungsbolzenschweißen.
Hubzündungsbolzenschweißen
Das Hubzündungsbolzenschweißen zeichnet sich durch eine Zündung des Lichtbogens nach dem Anheben des Bolzens vom Werkstück aus. Dadurch werden beide Elemente kleinflächig aufgeschmolzen und gehen durch anschließendes Aneinanderpressen und Auskühlen eine feste Verbindung ein.
Die wichtigsten Parameter für diese Variante sind der Schweißstrom, die Schweißzeit, der Hub (die Lichtbogenlänge) und der Überstand (das Eintauchmaß).
Spitzenzündungsbolzenschweißen
Diese Technik setzt eine äußerst eng tolerierte Zündspitze am unteren Ende des Bolzens voraus.
Das Verfahren lässt sich wiederum in zwei weitere Arten unterteilen.
Beim Spaltverfahren schmilzt die Zündspitze explosionsartig, verdampft dabei zum Teil und ein Knall ist zu hören. Der geöffnete Stromkreis induziert eine Spannung, die einen Lichtbogen zündet, der für kurze Zeit so stark ist, dass er die gesamte Fläche des Bolzens und Teile des Werkstücks aufschmilzt. Das kleine Schweißbad reicht aus, um die Elemente zu verbinden.
Das Kontaktverfahren verläuft ähnlich, jedoch hat der Bolzen bereits zu Beginn des Schweißvorgangs Kontakt zum Bauteil.
Die extrem kurze Schweißzeit und Einbrenntiefe macht es möglich, Bolzen auf dünne Materialien von nur 1 bis 1,5 mm Stärke zu schweißen.
Der Schutz des Schweißbades
Der Schutz des Schweißbades erfolgt entweder durch Schutzgas, oder wird durch einen Keramikring um den Bolzen realisiert.
Das Verfahren kann allerdings auch völlig ohne Schutzgas auskommen.
Laserschweißen – längst kein Science-Fiction Schweißverfahren mehr
Das Laserschweißen nutzt einen gebündelten Lichtstrahl, der das Material punktuell aufschmilzt. Dieses Verfahren eignet sich für Fertigteile, da der Wärmeeintrag sehr gering ist und weniger Spannungen im Material auftreten. Meist schützen Argon und andere inerte Gase das Schweißbad vor Oxidation und Verunreinigungen.
Es zeichnet sich durch eine hohe Schweißgeschwindigkeit und eine schmale und schlanke Schweißnaht aus. Laserschweißen wird vor allem zum Verbinden von Bauteilen eingesetzt, die mit geringem thermischen Verzug gefügt werden müssen. So wird das Verfahren zum Beispiel beim Bearbeiten von Messing, Aluminium, Stahl oder Thermoplasten eingesetzt.
Laserstrahlschweißen funktioniert manuell, halb- und vollautomatisch. Ein Arbeiter führt beim manuellen Laserstrahlschweißen den Draht mit der Hand zu und kann den Prozess durch ein getöntes Binokular beobachten. Die Steuerung halbautomatischer Anlagen geschieht mittels Joystick. Vollautomatische Maschinen nutzen CNC-Programme und fahren festgelegte Wege ab.
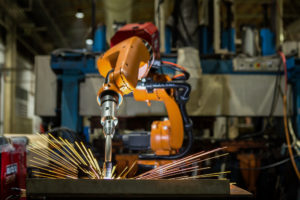
Formieren (Wurzelschutz)
Bei hochlegierten Stählen wir die Methode des Formierens bzw. Wurzelschutzes angewendet. Durch die Verwendung von inerten (Argon, Stickstoff) oder wasserstoffhaltigen Formiergasen (Stickstoff-Wasserstoff Gemisch) werden beim Formieren die Luftgase wie Sauerstoff und Stickstoff verdrängt.
Ohne den Einsatz des Formierverfahrens würde die Schweißnahtwurzel und der folgende Nahtbereich durch die Aufnahme von Sauerstoff, der sich in der Umgebung befindet, oxidieren. Hier sind eine schlechte Wurzelausbildung, eine raue Oberfläche und ein generell schlechtes äußeres Erscheinungsbild des Schweißens die Folge. Doch Formieren hat nicht nur Auswirkungen auf das Aussehen des Ergebnisses. Formieren fördert außerdem die Korrosionsbeständigkeit, was das Ergebnis qualitativ hochwertiger macht.
Das Unterpulverschweißen – Schweißverfahren mit Pulverzugabe
Die Schwerindustrie wendet das UP-Schweißen aufgrund seiner Wirtschaftlichkeit beim Fügen dickerer Bleche und Konstruktionen an.
Die Werkstücke werden durch einen Lichtbogen verschweißt. Dieser schmilzt automatisch zugeführtes, grobkörniges Pulver auf, welches sich dann als flüssige Schlacke auf die frische Naht legt und sie vor Umwelteinflüssen schützt. Eine Draht- oder Bandelektrode dient als Zusatz.
Unterpulverschweißen erfreut sich großer Beliebtheit im Schiffs- und Schienenfahrzeugbau sowie im Windkraftanlagenbau.
Das Verfahren ist schnell, es entstehen verhältnismäßig wenig Schadstoffe und die Spaltüberbrückbarkeit ist ausgezeichnet.
Diese Schweißtechnik kennt mehrere Arten, die sich folgendermaßen unterscheiden:
Eindrahtschweißen
Es ist die am häufigsten angewandte Methode und zeichnet sich durch eine hohe Abschmelzleistung aus. Meistens nutzt der Schweißer Gleichstrom und das feine Ende einer Drahtelektrode von 2 bis 4 mm Durchmesser und einer Länge von 20 bis 40 mm (Stick-Out).
Die Abschmelzleistung steigt, sobald er einen kleineren Durchmesser bei gleichbleibender Stromstärke nutzt. Zudem ergibt sich dadurch ein tieferer Einbrand.
Doppeldrahtschweißen
Das UP-Doppeldrahtverfahren (auch Twin genannt) nutzt zwei Drahtelektroden mit kleinerem Durchmesser. Beide sind an eine Gleichstromquelle angeschlossen und befinden sich maximal 15 mm voneinander entfernt. Die Abschmelzleistung beim Twin-Verfahren erhöht sich um bis zu 30 %. UP-Doppeldrahtschweißen verbessert die Spaltüberbrückbarkeit, die Schweißgeschwindigkeit und zeichnet sich durch äußerst stabile Schweißnähte aus.
UP-Bandschweißen
Dieses Verfahren unterscheidet sich vom UP-Eindrahtschweißen lediglich durch eine bandförmige Elektrode. Das UP-Bandschweißen findet Verwendung beim Plattieren; ein Verfahren, bei dem höherwertige Metalle auf weniger hochwertige Metalle aufgebracht werden. Temperatur und Druck sorgen für eine unlösbare Verbindung.
UP-Tandemschweißen
Das UP-Tandemschweißen erhöht die erreichbare Schweißgeschwindigkeit ein weiteres Mal. Bis zu sechs aufeinanderfolgende Elektroden arbeiten direkt nacheinander. Jede Elektrode, ausgestattet mit einer eigenen Stromquelle, besitzt eine Vorschubeinheit, um den Draht zuzuführen. Die erste Drahtelektrode, betrieben mit Gleichspannung, sorgt für einen tiefen Einbrand, die nachfolgenden, betrieben mit Wechselstrom, füllen diesen auf. Die letzte Elektrode bewirkt eine breite Naht mit einer hohen Oberflächengüte.
Das Widerstandsschweißen Schweißverfahren
Wenn Sie eine Bandsäge in Ihrer Werkstatt haben oder eine solche noch aus der Ausbildung kennen, dann sind Sie mit dem Widerstandsschweißen bereits vertraut.
Elektrisch leitfähige Werkstoffe lassen sich mittels Widerstandsschweißen verbinden. Haben die zu verbindenden Elemente die Schweißtemperatur erreicht, wirkt auf die Fügestelle eine Kraft, bis die Schmelze erstarrt. Diese Schweißtechnik kennt ebenfalls mehrere Varianten:
Widerstandspunktschweißen
Insbesondere im Fahrzeug- und Karosseriebau findet dieses Verfahren zum Verbinden von Blechen Anwendung. Unterschiedliche Metalle und Metallkombinationen können auf diese Art verschweißt werden. Widerstandspunktschweißen wird in der Elektroindustrie zur Fertigung von Kondensatoren, Relais und anderen elektronischen Bauteilen verwendet.
Den zu verschweißenden Teilen wird während einer Krafteinwirkung über Elektroden Strom zugeführt. Die Widerstandserwärmung erhitzt die Werkstücke auf Schweißtemperatur und an der Berührungsstelle verbinden sich die beiden Elemente. Nach dem Erstarren sind sie verschweißt.
Alle Verfahren dieser Schweißtechnik sind energieeffizient, benötigen kein Zusatzmaterial und sorgen für geringen Materialverzug.
Widerstandsbuckelschweißen
Zunächst wird eines der zu verschweißenden Bauteile mit einem Schweißbuckel besetzt. Die Elektroden pressen dieses und das andere Bauteil zusammen, während ein starker Strom zugeführt wird. Dadurch schmilzt der Schweißbuckel und die Metalle verbinden sich.
Drahtgeflechte und Gitter können an den überlappenden Stellen durch ihre Form bereits einen Schweißbuckel besitzen, sodass dieser nicht extra aufgelegt werden muss.
Widerstandsrollnahtschweißen
Das Widerstandsrollnahtschweißen basiert auf dem gleichen Prinzip wie das Widerstandspunktschweißen. Die Elektroden sind jedoch rollenförmig und führen die zu verschweißenden Bleche. Durch die Bewegung und gleichmäßigen Druck bei gleichbleibender Stromstärke ergibt sich eine durchgehende Schweißnaht zwischen den Bauteilen.
Welche persönliche Schutzkleidung (PSA) benötige ich für welches Schweißverfahren?
Die Berufsgenossenschaft schreibt je nach Verfahren und Situation verschiedenste Schutzkleidungen und -einrichtungen vor.
Generell ist immer eine getönte Schutzbrille, ein Schweißhelm oder ein Schweißschirm zum Schutz der Augen zu verwenden. Verblitzte Augen bereiten große Schmerzen und können sogar zur Erblindung des Schweißers führen.
Schwer entflammbare Kleidung wird stets hochgeschlossen getragen. Sicherheitsschuhe und besonders beim Gasschweißen auch Schienbeinschoner verhindern schwerste Verbrennungen. Ein Lendenschurz schützt vor der auftretenden Strahlung beim Schweißen.
Lärm und Gehörschutz bei fast allen Schweißverfahren essentiell
Lärmschwerhörigkeit ist laut DGUV bei Schweißtätigkeiten die häufigste Berufskrankheit. Schaut man sich die Schallpegel der der verschiedenen Schweißverfahren an, sieht man, dass die meisten von ihnen sehr laut sind.
So besteht ab einem Beurteilungspegel von 80dB(A) die Pflicht, dass der Arbeitgeber entsprechenden Schallschutzmittel zur Verfügung stellen muss. Ab dieser Schwelle gilt es auch, dem Mitarbeiter medizinische Vorsorge anzubieten.
Ab 85dB(A) gilt für die Mitarbeiter eine besondere Verpflichtung zur Benutzung dieser Schallschutzmittel. Hier muss der Arbeitgeber eine regelmäßige medizinische Vorsorge durchführen.
Schweißverfahren | Schallpegel dB(A) (Anhaltswerte) |
---|---|
Plasmaschneiden | 100 – 110 |
Flammwärmen, Flammrichten | 90 – 100 |
Brennschneiden (Einzelbrenner) | 85 – 95 |
Schutzgasschweißen: MIG, MAG | 82,5 – 95 |
Gasschweißen | 75 – 94 |
Lichtbogenhandschweißen | 80 – 90 |
Unterpulverschweißen | 75 – 85 |
Schutzgasschweißen: WIG | 70 – 75 |
Daneben besteht für Schweißer ein erhöhtes Risiko an Atemwegserkrankungen zu leiden. Achten Sie bei entsprechenden Schweißarbeiten auf ausreichende Absaugsysteme, um sich vor Feinstaub zu schützen.
Im Zweifel gibt die Berufsgenossenschaft Ihnen genaue Anweisungen zum sicheren Umgang mit den verschiedenen Schweißverfahren.
Welche Schweißverfahren benötigen Schutzgas?
Das Schutzgas schirmt das Schmelzbad sowie den Lichtbogen vor Stickstoff, Sauerstoff und Wasserstoff ab. Dadurch werden Poren und Einschlüsse in der Schweißnaht verhindert. Der Schutz vor dem Sauerstoff in der Umgebungsluft verhindert zudem das Verbrennen und Oxidieren.
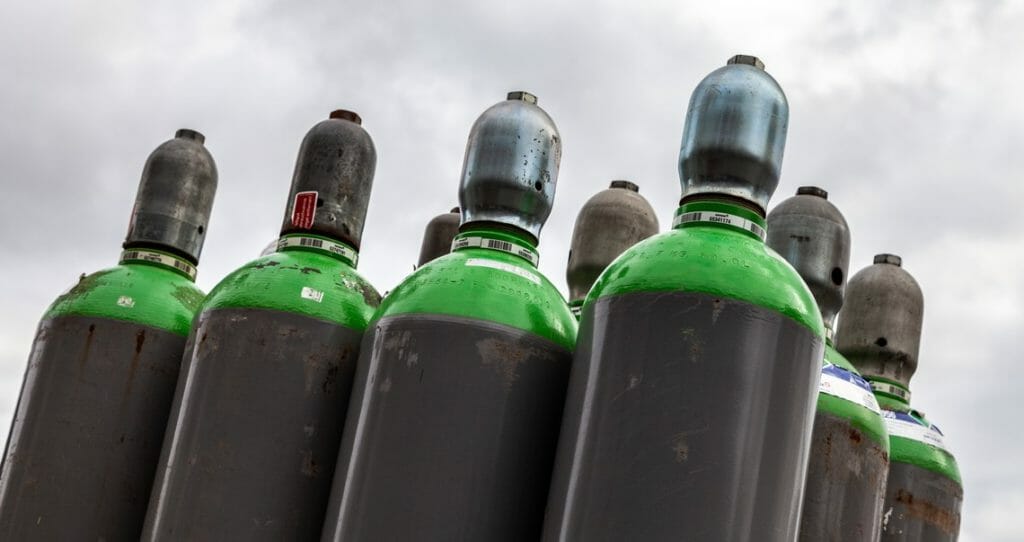
Besonders für hochlegierte Stähle und Leichtmetalle benötigen Sie entsprechende Schutzgase, um qualitativ hochwertige Schweißnähte zu produzieren.
Welche Schutzgase brauche ich für welches Schweißverfahren?
Grundsätzlich unterscheidet man Schutzgase beim Schweißen in aktive und inerte Schutzgase. Beim Metall-Aktivgas-Schweißen (MAG-Schweißen) soll das Aktivgas in der Schutzgasmischung explizit mit dem Werkstück reagieren. Die Schutzwirkung des Inertgas vor atmosphärischen Gasen bleibt vorhanden und die Reaktion kann genau kontrolliert besser. Die verwendeten Gase, meist reines Kohlendioxid oder Schweißgas Mischungen auf Basis von Argon, beeinflussen aktiv das Schweißergebnis. Ihr Zusatz beeinflusst die Stabilität des Lichtbogens, das Einbrandverhalten und letztlich auch die Struktur des Werkstücks.
Inerte Schutzgase unerlässlich beim MIG-Schweißen und WIG-Schweißen
Gilt es, eine Reaktion der Außenluft gänzlich zu vermeiden, kommen inerte Schutzgase zum Einsatz. Sie verdrängen die atmosphärische Luft und damit alle reaktionsfähigen Elemente rund um die Schweißnaht. Im Gegensatz zu Aktivgasen kommt es hier zu keinerlei Reaktion. Das garantiert das gewünschte Schweißergebnis und verhindert schädliche Außeneinflüsse auf die Schweißnaht.
Geeignete Schutzgase zum Schweißen nach ISO 14175
Nachfolgend haben wir die verschiedenen Schweißgase in einer Tabelle zusammengefasst. Die Veränderungen zur DIN EN439 sind hier schon eingetragen.
Übersicht geeigneter MAG-Schweißgase und deren Zusammensetzung
Metall-Aktivgas-Schweißen erfordert oxidierende Mischgase, die jeweils in Untergruppen eingeteilt sind. Die Gruppe C ist Kohlendioxid.
Gruppe | Kennzahl | CO2 | O2 | Ar | He | H2 | N2 | Bemerkung |
M1 | 1 | > 0 bis 5 | – | Rest* | – | > 0 bis 5 | – | schwach oxidierend |
2 | > 0 bis 5 | – | Rest* | – | – | – | schwach oxidierend | |
3 | – | > 0 bis 3 | Rest* | – | – | – | schwach oxidierend | |
4 | > 0 bis 5 | > 0 bis 3 | Rest* | – | – | – | schwach oxidierend | |
CO2 | O2 | Ar | He | H2 | N2 | |||
M2 | 0 | > 5 bis 15 | – | Rest* | – | – | – | |
1 | > 15 bis 25 | – | Rest* | – | – | – | ||
2 | – | > 3 bis 10 | Rest* | – | – | – | ||
3 | > 0 bis 5 | > 3 bis 10 | Rest* | – | – | – | ||
4 | > 5 bis 15 | > 0 bis 3 | Rest* | – | – | – | ||
5 | > 5 bis 15 | > 3 bis 10 | Rest* | – | – | – | ||
6 | > 15 bis 25 | > 0 bis 3 | Rest* | – | – | – | ||
7 | > 15 bis 25 | > 3 bis 10 | Rest* | – | – | – | ||
CO2 | O2 | Ar | He | H2 | N2 | |||
M3 | 1 | > 25 bis 50 | – | Rest* | – | – | – | |
2 | – | > 10 bis 15 | Rest* | – | – | – | ||
3 | > 5 bis 50 | > 8 bis 15 | Rest* | – | – | – | ||
C | 1 | 100 | – | – | – | – | – | stark oxidierend |
2 | Rest | > 0 bis 30 | – | – | – | – | stark oxidierend |
* Der Argon Anteil kann teilweise oder vollständig durch Helium ersetzt werden
Zusammensetzung geeigneter Schutzgase für WIG-Schweißen, Plasmaschweißen und Wurzelschutz
Reduzierende und inerte Schutzgase kommen beim Wolfram-Inertgas-Schweißen, Plasmaschweißen und zum Wurzelschutz, dem Formieren, zum Einsatz. Bei reduzierenden Schutzgasmischungen kommen Argon und Wasserstoff als Mischgas zum Einsatz.
Gruppe | Kennzahl | CO2 | O2 | Ar | He | H2 | N2 | Bemerkungen |
R | 1 | – | – | Rest* | – | > 0 bis 15 | – | reduzierend |
2 | – | – | Rest* | – | > 15 bis 50 | – | reduzierend | |
I | 1 | – | – | 100 | – | – | – | inert |
2 | – | – | – | 100 | – | – | inert | |
3 | – | – | Rest | > 0 bis 95 | – | – | inert |
*Der Argon Anteil kann teilweise oder vollständig durch Helium ersetzt werden
Schutzgase zum Plasmaschweißen und Wurzelschutz (Formieren)
Hier kommt vor allem der reaktionsträge Stickstoff zum Einsatz. Bei bestimmten Anwendungen wird noch anteilig Wasserstoff hinzugefügt.
Gruppe | Kennzahl | CO2 | O2 | Ar | He | H2 | N2 | Bemerkungen |
N | 1 | – | – | – | – | – | 100 | reaktionsträge |
2 | – | – | Rest* | – | – | > 0 bis 5 | ||
3 | – | – | Rest* | – | – | > 5 bis 50 | ||
4 | – | – | Rest* | – | > 0 bis 10 | > 0 bis 5 | ||
5 | > 0 bis 50 |
*Der Argon Anteil kann teilweise oder vollständig durch Helium ersetzt werden