Als Laserschneiden oder auch Laserstrahlschneiden wird das Durchtrennen von Material durch eine gepulste oder kontinuierliche Laserstrahlung definiert. Gefragt ist das Verfahren insbesondere in Bereichen, in denen eine besonders präzise und schnelle Bearbeitung komplexer Umrisse entscheidend ist.
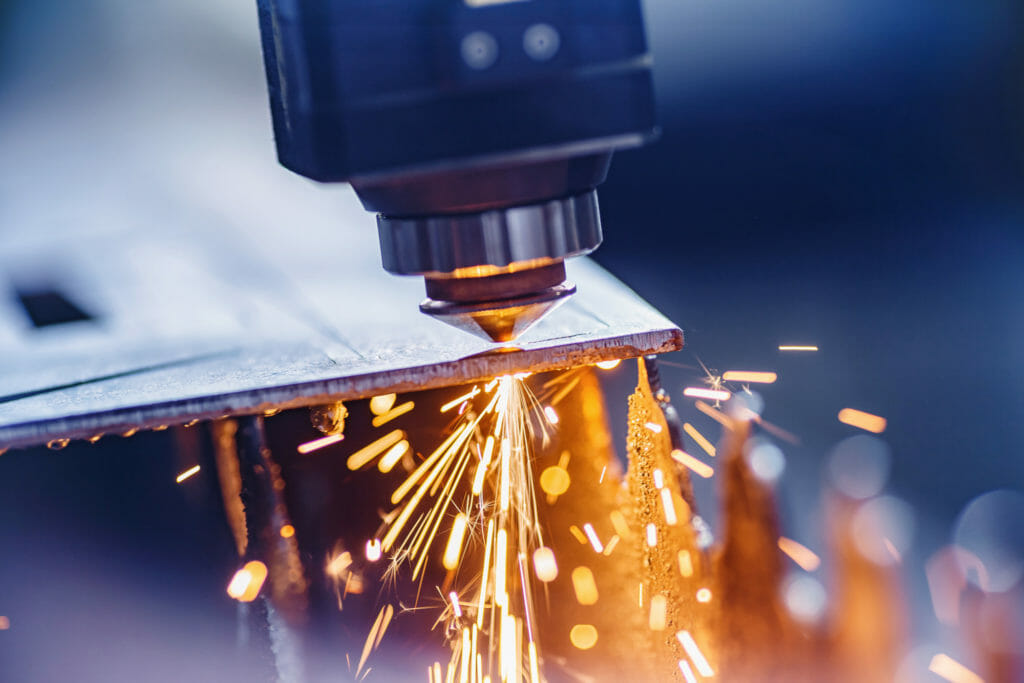
Mit dieser Schneidetechnik lassen sich auch Durchbrüche in 3 Dimensionen ausführen, und es kann fast berührungsfrei gearbeitet waren. Auch bei kleinen Produktionseinheiten erweist sich die Technik im Vergleich mit anderen Techniken als sehr wirtschaftlich. Deshalb ist Laserschneiden in Gewerbe und Industrie häufig in der Anwendung. Hier werden Möbelteile, Karosserieteile, Verblendungen, Formteile, Trägerelemente, Halterungen, Rohr- und Rundteile bevorzugt professionell mit Lasern geschnitten.
Die Themen im Überblick
- Laserschneiden – Was ist das und wie funktioniert es?
- Welche Verfahren gibt es beim Laserschneiden?
- Laserschneiden – Die Technik
- Wo wird Laserschneiden in der Industrie angewandt?
- Lasterstrahlschneiden – Kosten im Überblick
- Arbeitsschutz beim Laserschneiden essentiell
- Laserschneiden – Vorteile und Nachteile in der Übersicht
- Fazit
Laserschneiden – Was ist das und wie funktioniert es?
Die Basis der Technik reicht zurück in die 1960er Jahre. Damals kam es zu praktischen Anwendungen der bis dahin nur theoretisch beschriebenen Lasertechnik. Seiner Natur nach ist das Laserstrahlschneiden ein thermisches Trennverfahren. Ein Laserstrahl wird so intensiv auf eine Materialoberfläche geleitet, dass das Material schmilzt. Je nach Temperatur kann es auch zur Verdampfung des Ursprungsmaterials kommen.
Der Ablauf des Laserstrahlschneiden
Zunächst trifft der Laserstrahl punktförmig auf die Arbeitsfläche. Erst wenn er das Material vollständig durchdrungen hat, beginnt der Schneideprozess. Der Laser fährt über den gewünschten Umriss und durchtrennt das gesamte Material. Prozessgase führen zu noch besseren Ergebnissen. Als Gase werden Sauerstoff und Stickstoff, seltener Argon oder Helium eingesetzt. Die Gase kommen jeweils bei den unterschiedlichen Verfahren des Laserschneidens zum Einsatz. Weitere Ausführungen folgen dazu bei den Schneideverfahren.
Welche Verfahren gibt es beim Laserschneiden?
Die beiden Hauptverfahren beim Laserschneiden sind das Laserstrahlschmelzschneiden und das Laserstrahlbrennschneiden.
Laserstrahlschmelzschneiden
Die Schnittfuge entsteht bei diesem Verfahren durch fortlaufendes Aufheizen und folgendem Ausblasen des Werkstoffes mit einem inerten Gas. Hier kommt überwiegend Stickstoff, manchmal aber auch Argon oder Helium zum Einsatz. Das Gas steht einer Oxidation der Oberfläche entgegen. Diese Methode ist insbesondere dann gefragt, wenn es um exakte und oxidfreie Schnittkanten bei Edelstahl geht. Auch Aluminiumlegierungen und nicht-eisenhaltige Metalle werden auf diese Weise geschnitten. Normaler Baustahl kann bei Dicken bis 10 mm mit Stickstoff getrennt werden.
Zusätzliche Nachbearbeitung nach Laserschneiden meistens nicht mehr nötig
Hier entfällt eine Nachbearbeitung durch eine folgende Lackierung oder Beschichtung. Charakteristisch bei dem Verfahren ist die hohe Schnittqualität, weil sich auf den Schnittkanten kaum Riefen oder Grate bilden. Die Schnittqualität kann beeinflusst werden durch die Ausrichtung des optischen Fokus auf das Werkstück, durch die Vorschubgeschwindigkeit, die Leistung des Lasers und den Schneidgasdruck.
Laserstrahlbrennschneiden
Brennschneiden kommt seit jeher zum Schneiden von Metallen mit Eisen in Betracht. Kennzeichnend ist eine Erhitzung des Werkstoffes. Sie wird so intensiviert, dass das Material seine Entzündungstemperatur erreicht und über Zugabe von Sauerstoff verbrennt. Beim Verbrennen entsteht Energie, die den gesamten Schneidevorgang unterstützt. Es entsteht außerdem Eisenoxid, das von einem Sauerstoffstrahl ausgeblasen wird. Voraussetzung für den Einsatz dieses Verfahrens ist, dass Werkstoffe bearbeitet werden, bei denen die Zündtemperatur unterhalb der Schmelztemperatur bleibt.
Weitere Laserschneide-Verfahren
Es gibt noch einige andere Laserstrahl Schneide-Verfahren. Neben dem Ritzen und dem thermischen Laserstrahl-Separieren ist Laserstrahlsublimierschneiden mit seinem Verdampfungseffekt bekannt. Die hier prozessierten Werkstoffe, wie zum Beispiel Holz oder bestimmte Kunststoffe, schmelzen nicht, sondern verdampfen sofort. Das Schutzgas hat hier die Rolle, anstelle der Schlacke die entstehenden Dämpfe aus der Schnittfuge zu verdrängen.
Die Laserschneiden Technik – So schneidet der Laser Stahl, Edelstahl, Kunststoff und Kupfer
Laserschneid-Geräte bestehen aus der Quelle für den Laserstrahl, der Führung für den Strahl und dem Fokussierkopf mit seiner Optik. Ebenfalls integriert ist eine Schneidedüse. Die Optik hat die Aufgabe, den Laserstrahl zu bündeln und damit die zum Schneiden erforderliche Intensität zu erreichen. Anlagen mit CO2-Lasern haben hier regelmäßig eine unbewegliche Laserstrahlquelle und eine bewegliche Optik.
Unterschiedliche Laser für verschiedene Materialien
Die präzisen Schnitte werden vor allem durch die intensive Fokussierung erreicht. Es kommen unterschiedliche Laser für die jeweiligen Materialien zum Einsatz. Auch die Dicke des jeweiligen Materials spielt eine Rolle für den zu wählenden Laser. Wärmeleitende Metalle wie etwa Kupfer lassen sich kaum mit einem CO2-Laser schneiden. Neben der grundsätzlich starken Hitzereflektion nimmt der Werkstoff zusätzlich auch die Hitze des Lasers zu schnell auf und verteilt sie großflächig. Hier kommen meist gepulste Faserlaser zum Einsatz.
Einstechen in den Werkstoff als wichtiger Zwischenschritt
Das Kernstück des gesamten Verfahrens ist das Einstechen des Lasers in den Werkstoff. Dieser Vorgang kann die meiste Zeit in Anspruch nehmen, weil mit einem gepulsten Strahl und einer verringerten Leistung vorgegangen werden muss. Es könnten sonst reflektierende Metallspritzer entstehen. Moderne automatisierte Maschinen zum Laserschneiden verfügen über dafür über eine Vielzahl unterschiedlicher Sensoren. Mit ihnen wird der Durchstich vor Beginn der Arbeiten genau geplant und konzeptioniert.
Hohe Temperaturunterschiede verhärten die Schnittkanten
Es wird außerdem sichergestellt, dass nicht mit dem Schneiden begonnen wird, bevor das Material komplett durchstochen wurde. Obacht ist geboten, weil beim Schneiden von Stahl die Schnittkanten durch die hohen Temperaturunterschiede verhärten. Bei der weiteren Bearbeitung können diese Verhärtungen Probleme bereiten. Flache Werkstücke müssen auf einer Auflage liegen, die eine möglichst geringe Auflagefläche, kaum Reflexion und höchste Widerstandsfähigkeit gegen den Abtrag durch den Laser bietet.
Wo wird Laserschneiden in der Industrie angewandt?
Mit Lasern lässt sich nicht nur schneiden, sondern auch gravieren und markieren. Entsprechend groß sind die Einsatzbereiche in der industriellen Anwendung. Typische Anwendungsbereiche sind beispielsweise der Flugzeug- und Fahrzeugbau, die Herstellung von Dekorationen, Landmaschinen und Möbeln, die Produktion von Elektronikbauteilen und medizinischen Geräten. Grundsätzlich erweitern sich die Einsatzmöglichkeiten durch fortgeschrittene Technik und neu entwickelte Laser immer weiter. Ähnlich wie beim Laserschweißen lässt sich durch Automatisierung von Laserschneideprozessen ein sehr hohes Maß an Genauigkeit gepaart mit hohen Fertigungsgeschwindigkeiten erreichen.
Lasterstrahlschneiden – Kosten im Überblick
Bei den Kosten sind vor allem Anschaffungskosten für die Maschine selbst und die Maschinenlaufzeit maßgeblich. Die Leistung beim Laserschneiden berechnet sich nach der Maschinenlaufzeit. Je länger ein Laser im Einsatz ist, desto teurer wird die Bearbeitung. Man rechnet hier mit etwa 1 Euro pro Minute Maschinenlaufzeit und 60 EUR pro Stunde. Die Kosten für die Anschaffung einer Laserschneideanlage variieren je nach Größe, Leistung und Automatisierungsgrad. Große Anlagen können mit mehreren 100.000 EUR zu Buche schlagen. Auch kleinere Geräte sind nicht eben günstig.
Arbeitsschutz beim Laserschneiden essentiell
Geschnitten wird bei diesem Verfahren mit unsichtbaren Laserstrahlen. Dabei ist die Leistung der Laser sehr hoch. Menschliche Haut und Augen sind durch gestreute oder reflektierte Strahlenanteile gefährdet. Deshalb verfügen die Lasermaschinen regelmäßig über geschlossene Kabinen. Diese dürfen nur geöffnet werden, wenn der Laserstrahl abgeschaltet wurde. Dennoch ist die Gefahr von oft zunächst unerkannten Augenschäden hoch. Das liegt daran, dass die Kabinenumwandung mit steigender Leistung den Strahlen kaum Widerstand leisten kann.
Entstehende Dämpfe beim Laserschneiden
Bei Metallen entwickelt sich zudem Aerosol aus dem Material der Schnittfuge. Insbesondere wenn Stahllegierungen geschnitten werden, können sich Nickel, Chrom oder Kobalt in einatembare Aerosole verwandeln. Gefährlich ist in diesem Zusammenhang auch Berylliumkupfer. Gefahren lauern ebenso in anderen Materialien. Beispielsweise entstehen unter Umständen gesundheitsgefährdende Stoffe beim Schneiden von organischen Materialien. Hier ist beispielsweise an Halogenwasserstoffe, Dioxine und Furane zu denken.
Abluftsysteme sind unerlässlich
Anlagen zum Laserschneiden müssen über Absaugungsanlagen verfügen. Damit wird der beim Schneiden entstehende Schmauch sofort abgeleitet, um unerwünschte Verfärbungen an der Schnittkante zu verhindern. Ebenso können gefährliche Aerosole evakuiert werden. Außerdem muss die Abluft Filter durchlaufen, die gegen Brände geschützt sind. Diese Umstände machen das Laserschneiden auch zu einer relativ teuren Technik.
Laserschneiden – Vorteile und Nachteile in der Übersicht
Gegenüber konventionellen Trennverfahren wie beispielsweise dem Stanzen hat das Laserschneiden verschiedene Vorteile, aber auch ein paar Nachteile.
Die Vorteile:
Vorzüge dieser Technik sind unter anderem die hohe Produktivität und Wirtschaftlichkeit. Material kann in hohem Maße ausgenutzt werden. Es ergeben sich regelmäßig abhängig vom Werkstoff sehr saubere, eher schmale Schnittkanten, die häufig nicht nachbearbeitet werden müssen. Man kann im selben Arbeitsgang schneiden und gravieren sowie kennzeichnen. Es sind beim Laserschneiden geringste Stückzahlen ab einem Stück wirtschaftlich. Je nach Anlage können die verschiedensten Materialien mit Laser geschnitten werden.
Die Nachteile:
Zu den Nachteilen muss man die hohen Anlagenkosten, erhöhte Anforderungen im Arbeitsschutz und einen hohen Wert beim Gasverbrauch rechnen. Helium ist beispielsweise sehr teuer. Außerdem sind Anwendungen beim Laserschneiden eher energieintensiv.
Laserschneiden Vorteile und Nachteile auf einen Blick:
Vorteile
hohe Produktivität und Wirtschaftlichkeit
Sehr effektive Materialnutzung
Saubere, schmale Schnittkanten
Kaum oder teilweise sogar keine Nachbearbeitung nötig
Schon bei geringsten Stückzahlen wirtschaftlich
Anwendbar mit verschiedensten Materialen
Nachteile
Hohe initiale Kosten für die Laserschneide-Anlage
Hohe Anforderungen an den Arbeitsschutz
Sehr energieintensives Verfahren
Fazit:
Wer bereit ist, in eine Laseranlage zu investieren, verfügt mit dem Laserschneiden über eine exzellente und wirtschaftliche Schneidetechnik für verschiedenste Materialien. Gerade im Zusammenhang mit der zunehmenden Automatisierung von Produktionsanlagen und den Anforderungen an Just-in-Time Produktionen mit kleinen Stückzahlen überzeugt das Laserschneiden mit seinen vielen Vorzügen im Vergleich mit Techniken wie dem Stanzen.